-
PDF
- Split View
-
Views
-
Cite
Cite
Philipp Dancker, Karl Glas, Martina Gastl, Potential utilisation methods for brewer’s spent grain: a review, International Journal of Food Science and Technology, Volume 60, Issue 1, January 2025, vvae022, https://doi.org/10.1093/ijfood/vvae022
- Share Icon Share
Abstract
Brewing is an energy- and water-intensive operation. Efforts to increase the resource efficiency of a brewery usually only focus on the production itself in the form of internal measures. Wastewater and residual materials are usually neglected, although they have a high potential for reuse in a circular economy and energy recovery. To be prepared for a sustainable future, breweries need to act. This review gives an overview over the possibilities for the brewing industry to effectively utilise their highly abundant and perishable brewer’s spent grain to eliminate a potentially environmentally harmful disposal, redesign their biowaste into a biosorbent, and contribute their part in a circular economy.
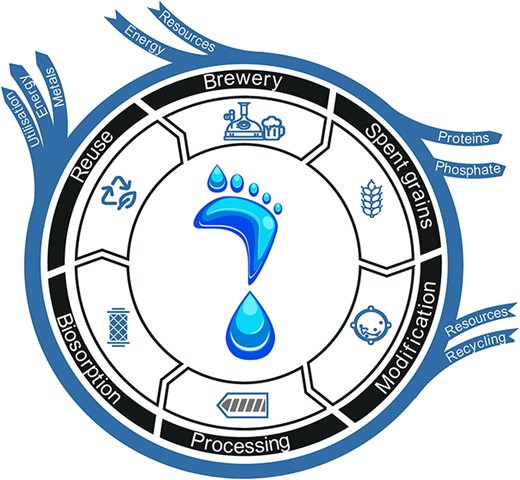
Introduction
In 2021, the worldwide beer production was 186 GL (Statista Inc, 2023). About 20 kg of wet brewer’s spent grain (BSG) accrue for every 100 L of beer produced. This amount represents 85% (w/w) of beer-specific waste, and it is therefore the largest proportion by mass (Herfellner et al., 2006; Mussatto et al., 2006). Depending on the brewing style, gravity, and technology, this ratio can differ a little. Still, it results in a yearly production of about 7.2 Mt BSG in China, 3.9 Mt BSG in the United States, 3.4 Mt BSG in the European Union (EU), 2.8 Mt BSG in Brazil, 0.7 Mt BSG in Africa, or 37.8 Mt BSG worldwide (Barth & Meier, 2022; Maqhuzu et al., 2021; Mussatto et al., 2006; Sganzerla et al., 2021b; Stojceska & Ainsworth, 2008). BSG is a problematic waste with its high-moisture content of up to 80%(w/w) directly from production, microbial susceptibility, unsuitable pH value for aerobic stabilisation, and non-optimal C/N ratio for direct composting (Assandri et al., 2020). A brewery needs a fast distribution method for BSG to continue production. Therefore, it can be assumed that BSG is an abundant and cheap substrate with a renewable source that needs a valorisation and recycle process to counteract its low market value and evade an ecologically harmful disposal. Now BSG is mainly used as animal feed but due to its instability this is only feasible if a livestock farm is near the brewery and in need for the feed. In this review, possible valorisation applications will be presented and evaluated. For this review, those applications are divided into four main categories: biorefinery, functional materials, energy recovery, and nutritional. Under those categories, the usage of BSG to produce biogas, biosorbents, brick additives, food additives, or paper, as well as microbiological, chemical and physical degradation, fermentation, and alteration to form useful materials is discussed. The same dilemma hovers over those application as with any application involving the transformation of a food or feed source into a technical operating material, to feed a human, animal, or a technical process (Figure 1) (Andechs, 2021; Augustiner, 2022; Brauerei S. Riegele I. R. K., 2022; Lammsbräu, 2023; München, 2020).
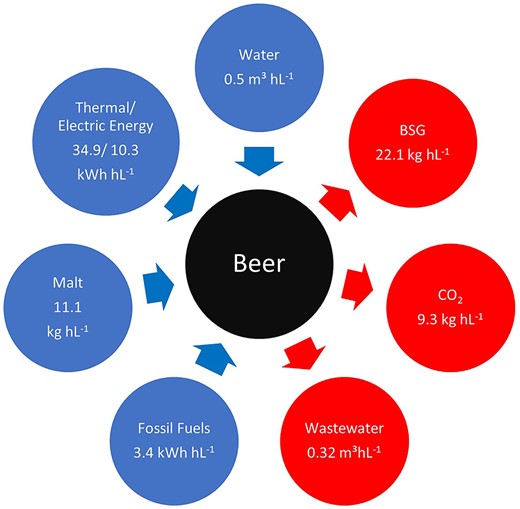
Averaged resource flow from the sustainability reports of seven German breweries.
Constituents of BSG
BSG is an abundant and cheap material but with a heterogeneous content, non-degradable protein, fermentable sugar, microbial load, and high moisture of 70%–80%(w/w) out of process (Vieira et al., 2014; Westendorf & Wohlt, 2002). The pretreatment for further processing can be highly expensive or complicated, when the BSG needs to be dried or transported. Just in a few days without conservation, the self-decomposition starts (Klemes et al., 2008), and without drying, the BSG undergoes microbial and chemical degradation (Robertson et al., 2010). A relatively cheap way to dry the BSG is by pressing down to a moisture content of about 10%(w/w) (Ivanova et al., 2017). Alternatively, it has to be collected in a timely manner from the brewery for further processing. Table 1 and Figure 2 show the major components of air-dry BSG in %(w/w).
Constituents of air-dry brewer’s spent grain in %(w/w) (Herfellner et al., 2006).
Constituent . | Barley draff . | Wheat draff . | Fine . | Medium . | Coarse . |
---|---|---|---|---|---|
Protein | 20–22 | 20–22 | 31.19 | 25.28 | 23.22 |
Fat | 16–18 | 15–18 | n.a. | n.a. | n.a. |
Starch | 0.8–1.0 | 0.6–1.0 | n.a. | n.a. | n.a. |
Hemicellulose | 25–30 | 35–40 | 62.40 | 66.20 | 75.30 |
Cellulose | 18–20 | 14–16 | |||
Lignin | 8–10 | 4–7 | |||
Ash | 3–4 | 3–4 | 3.57 | 3.66 | 3.76 |
Moisture | n.a. | n.a. | 7.6 | 6.8 | 6.7 |
Herfellner et al. (2006) | Mussatto and Roberto (2006) |
Constituent . | Barley draff . | Wheat draff . | Fine . | Medium . | Coarse . |
---|---|---|---|---|---|
Protein | 20–22 | 20–22 | 31.19 | 25.28 | 23.22 |
Fat | 16–18 | 15–18 | n.a. | n.a. | n.a. |
Starch | 0.8–1.0 | 0.6–1.0 | n.a. | n.a. | n.a. |
Hemicellulose | 25–30 | 35–40 | 62.40 | 66.20 | 75.30 |
Cellulose | 18–20 | 14–16 | |||
Lignin | 8–10 | 4–7 | |||
Ash | 3–4 | 3–4 | 3.57 | 3.66 | 3.76 |
Moisture | n.a. | n.a. | 7.6 | 6.8 | 6.7 |
Herfellner et al. (2006) | Mussatto and Roberto (2006) |
Constituents of air-dry brewer’s spent grain in %(w/w) (Herfellner et al., 2006).
Constituent . | Barley draff . | Wheat draff . | Fine . | Medium . | Coarse . |
---|---|---|---|---|---|
Protein | 20–22 | 20–22 | 31.19 | 25.28 | 23.22 |
Fat | 16–18 | 15–18 | n.a. | n.a. | n.a. |
Starch | 0.8–1.0 | 0.6–1.0 | n.a. | n.a. | n.a. |
Hemicellulose | 25–30 | 35–40 | 62.40 | 66.20 | 75.30 |
Cellulose | 18–20 | 14–16 | |||
Lignin | 8–10 | 4–7 | |||
Ash | 3–4 | 3–4 | 3.57 | 3.66 | 3.76 |
Moisture | n.a. | n.a. | 7.6 | 6.8 | 6.7 |
Herfellner et al. (2006) | Mussatto and Roberto (2006) |
Constituent . | Barley draff . | Wheat draff . | Fine . | Medium . | Coarse . |
---|---|---|---|---|---|
Protein | 20–22 | 20–22 | 31.19 | 25.28 | 23.22 |
Fat | 16–18 | 15–18 | n.a. | n.a. | n.a. |
Starch | 0.8–1.0 | 0.6–1.0 | n.a. | n.a. | n.a. |
Hemicellulose | 25–30 | 35–40 | 62.40 | 66.20 | 75.30 |
Cellulose | 18–20 | 14–16 | |||
Lignin | 8–10 | 4–7 | |||
Ash | 3–4 | 3–4 | 3.57 | 3.66 | 3.76 |
Moisture | n.a. | n.a. | 7.6 | 6.8 | 6.7 |
Herfellner et al. (2006) | Mussatto and Roberto (2006) |
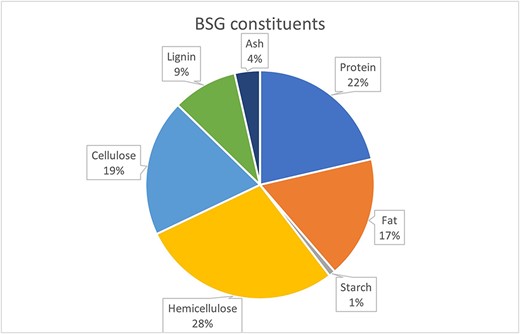
Constituents of BSG DW (Herfellner et al., 2006). BSG = brewer’s spent grain; DW = dry weight.
Lignocellulose
Cellulose, hemicellulose, and lignin are not stored separately in the cell wall. The cellulose is embedded into elementary fibrils enclosed by hemicellulose and lignin. This complex biological structure is called lignocellulose (LC) (Ludwig, 2014). Since every plant cell wall on earth has LC as an important main ingredient, it is the most abundant polymer on earth. Cellulose alone can occur in a crystalline or amorphous structure as well. It is a poly saccharide made of β-(1,4)-linked D-glucopyranose molecules condensed together to form a hemiacetal. Contrary to expectations because of the high content of hydroxyl functional groups, the cellulose molecule is not water soluble. The hydroxyl groups form strong hydrogen bonds with neighbouring oxygen atoms forming a chain with high-tensile strength (O’Connell et al., 2008). Hemicellulose is an amorphous polymer consisting of smaller chains with different kind of hexose and pentose sugars as well as their oxidised acid counterparts (Figure 3) (BLE, 2023). The amorphous structure makes the hemicellulose easier susceptible to chemical hydrolysis compared to crystalline cellulose (Figure 4) (Wyman et al., 2005). Lignin is manly composed of the three monolignols coniferyl alcohol, p-coumaryl alcohol, and sinapyl alcohol (Figure 5). The lignin polymer is covalently bound with hemicellulose. Those cross-links are the reason for the sturdiness and rigidity of wood and create impermeable cell wall against water and microbial attack. This high biochemical resistance of LC impedes further utilisation, and its structure and composition can be influenced by the plant itself, its biotic and abiotic stress, and even processing steps like the mashing conditions (Mussatto & Roberto, 2006; Vanholme et al., 2010).
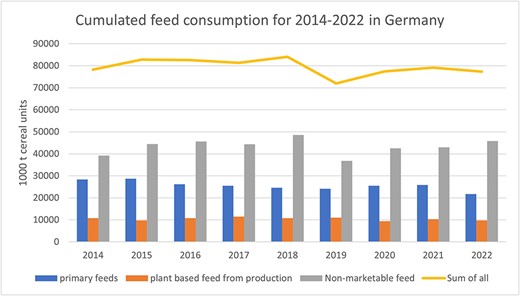
Cumulated feed consumption for 2014–2022 in Germany (BLE, 2023).

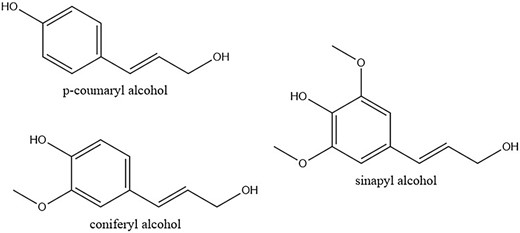
Biorefinery
A biorefinery valorises biological raw material with microorganisms into building-block chemicals, intermediates, polymers, energy, or a final product like a petroleum refinery. They are a key component in a circular and sustainable economy with their ability to upcycle and eliminate waste. The use of biological substrates to create chemical products reduces the dependency on fossil fuels and CO2 emissions. Preferably biological waste should be the substrate to maintain sustainability and to not interfere with the food production (De Bhowmick et al., 2018; de Jong et al., 2012; FitzPatrick et al., 2010). In general terms, the discussed biogas plant in Biogas section is a biorefinery as well. For this review, the term biorefinery focuses on the production of chemicals and is treated separately to the energy production of a biogas plant.
The composition of BSG, comprising carbohydrate and proteinaceous fractions, complicates subsequent processing steps due to the intricate polymeric lignocellulosic matrix, which can be valorised into distinct components separate from the protein fraction. Simultaneously, this opens up opportunities for multipurpose applications. If the anaerobic digestion (AD) is intentionally left incomplete through manipulating pH, temperature, and loading rate, it is possible to inhibit the methanogenesis and produce the intermediate products: short-chained organic acids, alcohols, and other platform chemicals to produce biofuels, bioplastics, fertiliser, or polyhydroxyalkanoates from a highly acidic dark fermentation digestate (Kleerebezem et al., 2015; Ospina-Betancourth et al., 2022; Peces et al., 2021; Ramos-Suarez et al., 2021; Venkata Mohan et al., 2016). With chemical synthesis and preparation similar to the paper industry, it is possible to separate the LC and produce bioactive compounds, e.g., activated carbon, lactic acid, phenolic acid, and xylitol (Mussatto et al., 2013). Many authors showed that it is possible to use the carbohydrate-rich fraction of BSG as biomass fuel for a biorefinery to produce ascorbic, lactic, and methylidenebutanedioic acid, butane-2,3-diol, butanol, and ethanol. An enzymatic, alkaline, or acid hydrolysis, or steam explosion pretreatment is needed to break down the structural LC from BSG into fermentable and saccharifiable molecules (Akermann et al., 2020; Banjo et al., 2018; Fernández-Delgado et al., 2019; López-Linares et al., 2020; Plaza et al., 2022; Pinheiro et al., 2019; Ravindran et al., 2019; Radosavljević et al., 2020; Rojas-Chamorro et al., 2020; Wagner et al., 2022; Weiermüller et al., 2021) (Figure 6).
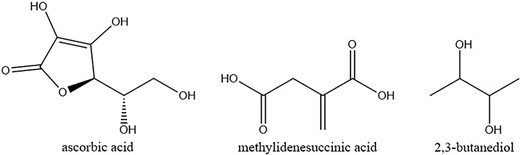
For most technical applications, the high-water content and microbial susceptibility of BSG are disadvantages which are flipped in biotechnology. BSG can be used as a substrate for the production of enzymes and value-added products with many different kinds of bacteria and fungi from the Aspergillus, Fusarium, Lactobacillus, and Bifidobacterium genera without the need for drying (Xiros & Christakopoulos, 2012).
Functional materials
Biosorbents
Climate change will lead to higher temperature and prolonged periods of drought in the world and especially Germany (Boeing et al., 2022), which emphasises the need for water reprocessing treatments to reduce wastewater (WW) and gain clean water sources. Through industrial processes, water gets contaminated with various kinds of chemicals, metals, pharmaceuticals, pesticides, by-products, auxiliary, and operating materials. One important clean-up tool is the adsorption for the removal of metals where adsorbents are used to reduce the solute content from a liquid. One important aspect for the environment and human health is the removal of toxic metals from industrial WW. Synthetic adsorbents like activated carbon, zeolites, silica gel, or aluminium oxides are expensive, and their production is not sustainable. Biosorbent is the technical generic term for adsorbents made of biomaterials, with or without, chemical, mechanical, or biological modification. Biosorbents in the form of algae, bacteria, fungi, spent grains, forest biowaste, or other agricultural waste are most abundant, sustainable, and inexpensive but with less adsorption capacity and secondary components. See Table 2 for an overview of biomaterials used for biosorbents. The main active component in the adsorption process of biosorbents is LC. Since the native form of the biosorbent material is a rather inefficient adsorbent, two procedures have been established to enhance the performance: pretreatment and modification. The pretreatment process involves washing the biomaterial with an acidic or alkaline solution or subjecting it to comminution. These steps activate binding surface sites, expose additional adsorption sites, and enhance the effective surface area by reducing particle size. The modification step introduces additional binding sites through esterification with organic or mineral acids, halogenation, and polymer grafting into the material (Hokkanen et al., 2016).
BSG with its high LC content can therefore be used as a biosorbent, which is already proven by some researchers (Carrasco et al., 2022; Li et al., 2012; Wierzba & Kłos, 2019). While the adsorption capacity cannot keep up with the technical adsorption materials, the cost can compensate for it. Technical adsorption materials are expensive materials compared to BSG. Publicly available prices for common technical adsorption materials from Merck are as follows: aluminium oxide 90 active basic for 82€ kg−1, silica gel for 107€ kg−1, < 20 μm zeolite powder for 622€ kg−1, and 4–12 mesh particle size activated carbon for 246€ kg−1 (Merck, 2024). BSG right out of the brewing process is sold for 0.02–0.05€ kg−1. The price varies greatly depending on whether the BSG is collected directly from the farmer or distributed via a specialised company (phone survey among German breweries). Prices are no constants but negotiable values so those numbers will change depending on the trading partners. Nevertheless, it will not be possible to close this gap and a valorisation factor of at least 1,000 between a technical adsorbents and BSG can be assumed.
Brick additive, packaging materials, and hydrothermal carbonisation
To increase the porosity in bricks and therefore improve their insulation properties, BSG or other high fibre products can be added to the brick firing as aggregates. The theoretical demand for such an aggregate would equal the total produced amount of BSG in Germany in 2005 (Russ et al., 2005; Weber, 2009). Other applications are the use of single constituents of BSG after a chemical or physical pretreatments and the separation for the productions of biomaterials (Qazanfarzadeh et al., 2023). Through artificial coalification under high pressure by direct steam injection, biochar can be made from BSG like from every other hydrocarbon biomass (Poerschmann et al., 2014). This process is called hydrothermal carbonisation (HTC). The biomass is injected with saturated steam at around 200 °C with pressures above 2 MPa for several hours. Through dehydration, decarboxylation, and polymerisation, the BSG biomass is converted into solid biochar with the associated properties (Funke & Ziegler, 2010; Kirtania, 2018). While the biomass of BSG itself is carbon neutral source, the HTC process is energy-intensive with corresponding emissions counteracting the sustainable and inexpensive approach.
The applications as brick additive, biomaterial, or biochar have in common that they are not exclusive for BSG and substitution with any other LC biomass is possible. The water content of BSG decreases the overall efficiency because of the energy demand of thermal drying and the production of problematic WW with press drying or chemical modification and separation of the different fractions of BSG for packaging. The protein fraction of BSG is too valuable as a nutritional source to be used as packaging material. Substitute cellulose products like saw dust are more suitable and easily available.
Energy recovery
Biogas
A brewery requires energy inputs, especially heat and electricity, for brewing, pasteurisation, fermentation, and refrigerated conditions. The supply of the required quantities of electricity and heat is responsible for greenhouse gas emissions and highly influence the operating cost. The production and consumption of self-produced biogas can reduce both and positively influence the environmentally friendly image of a brewery. Among several waste management technologies, AD is a promising method for converting wet wastes and solid residues into biogas for energy recovery on an industrial scale (Sganzerla et al., 2021a).
Biogas can be classified as any combustible gas produced by the fermentation of biomass. The main combustible contributors are methane (CH4) and hydrogen (H2). Beside that the biogas contains hydrogen sulphide (H2S), carbon dioxide (CO2), and ammonia (NH3) as by-products. The needed purification adds cost to the gasification, as well as the possibility of selling surplus CH4 into the natural gas grid. After a clean-up to food product specifications, CO2 emerges as a valuable resource for the carbonisation in the food industry or the brewery itself. Only CH4 and H2 can be used as a fuel for the generation of thermal energy in heating and steam boilers. Hydrogen fuel cells or combined heat and power plants can be utilised to cogenerate usable heat and electricity to increase the efficiency (Kaparaju & Rintala, 2013). The fermentation residue contains mineralised nitrogen, phosphate, and potassium which can be utilised as fertiliser (Buller et al., 2021). The operating and clean-up costs of a biogas plant decrease exponential with its capacity in m3 h−1. About 2–4 c kWh−1 can be reached at over 200 Nm3 h−1 biogas production depending on the kind of clean-up method: membrane, polyethylene glycol, pressure swing adsorption, amine, or pressure washing (Daniel-Gromke, 2019). It needs to exceed a threshold to break even with the purchasing prices of natural gas for a brewery which will be unattainable at current market prices for small breweries (about 100,000 hL year−1, see Equation 1) which are the majority in Europe. It is possible to ferment BSG alone or co-ferment it with WW, sewage sludge, wine vinasse, rice straw, and municipal waste (Atelge et al., 2020; Kim et al., 2013; Tena et al., 2020; Tyagi et al., 2014). Mixing different kinds of waste helps to adjust the C/N ratio, maintaining the optimal pH value and sustaining an optimal microbial community (Perez-Esteban et al., 2022). This enables the pooling of waste from several smaller breweries, food industries, and municipal waste management, which cannot maintain an own biogas plant and would profit indirectly in form of electricity, thermal energy, or income.
Rough estimate of the biogas production potential
Ruminal nitrogen balance (RNB) (Riemeier, 2004).
The fermentation process consists of four main stages: hydrolysis, acidogenesis, acetogenesis, and methanogenesis in which the complex organic matrix is decomposed into small molecules like H2, CH4, H2S, CO2, H2O, and NH3. Depending on the grade of incrustation and chemical nature of the plants organic matter, the decomposition will be retarded (Li et al., 2013; Lübken et al., 2010). The acid detergent lignin (ADL) and hemicellulose content of a plant can serve as predictors of biogas yield. Biogas yield exhibits a significant negative correlation with ADL content and a positive correlation with hemicellulose content. (Dandikas et al., 2014). LC is the most abundant renewable resource in the world, widely available and cheap, but its hydrolysis is usually incomplete due to its complex structure. The scientific literature describes several challenges in energy production by AD, especially incomplete conversion of recalcitrant high ADL materials such as BSG, which can be enhanced by chemical, mechanical, biological, or combined pretreatments (Buller et al., 2022; Dandikas et al., 2014; Hendriks & Zeeman, 2009; Kamusoko et al., 2019; Passos et al., 2015). In contrast to chemical processes, ultrasound does not produce waste but increases energy consumption, while biological pretreatment processes require more time. From a technical-economic point of view, the feasibility of a pretreatment method must be assessed on a case-by-case basis.
In a single-phase biogas reactor, all four stages of fermentation occur at the same time while bacteria and archaea metabolic pathways are intertwined with the substrates and products of the others (Angelidaki et al., 2009; Mittweg et al., 2012). Although the groups of microorganisms have a different optimal growth range, the microbiological steps are highly interdependent due to syntrophic and synergic effects (Bauer et al., 2008). High proteinaceous waste like BSG contains large amounts of nitrogen, which can poison the fermentation and generates high amounts of inorganic ammonia nitrogen (NH3, NH4+) (Sganzerla et al., 2022b).
In an anaerobic co-fermentation reactor, hydrogen yields of 9.55 ml H2 g−1 total volatile solids (TVS) can be reached with 17.5%(w/w) BSG in the substrate. With only WW, the yield is higher at 25.11 ml H2 g−1 TVS which is explained with an ammonia inhibition from the high nitrogen content in BSG. As fermentation by-products, short-chain organic acids are formed and acidify the sludge (Cieciura-Włoch et al., 2021). While acetic and butyric acid enhance the H2 production, propionic acid can be detrimental (Lovato et al., 2018). As seen, the fermentation can be modulated to produce desired results in CH4 and H2 yields. What remains as a problem is the exponential scaling with size which makes a biogas plant unattainable for small breweries and the highly reluctant proteinaceous LC matrix of BSG with its incomplete hydrolysis and ammonia inhibition.
Combustion
BSG has 70%–80%(w/w) water out of production which needs to be reduced to at least 60%(w/w) for direct combustion. If an organic substance is burnt, all the containing liquid water is turned into water vapour. The energy quantity required for this is the enthalpy of vaporisation ΔHvap and if not recovered reduces the heating value of the fuel. The reduction of the water content prior to combustion of the fuel is therefore a necessity but requires energy as well. The two main methods to reduce the water content are pressing and thermal drying. While pressing requires 0.019–0.100 kWh kg−1 dry weight (DW), there is a practical limit of about 40%(w/w) DW and the presswater emerges as a waste product with high chemical oxygen demand (COD). Thermal drying of BSG is possible up to 91%(w/w) DW, and no waste is generated but it needs at least 0.661 kWh kg−1 water as thermal energy (enthalpy of vaporisation for water) which makes it unfeasible. Pressed to 40%(w/w) DW BSG becomes a fuel comparable to firewood with a heating value of 4.9 to 5.3 kWh kg−1 DW (Gil-Castell et al., 2022) but with problematic flue gas that contains carbon monoxide (CO), nitrogen oxides (NOx), and sulphur oxides (SOx) through the high nitrogen and sulphur content and incomplete combustion which needs further cleaning (Weger et al., 2017). Without clean-up, nitrogen and sulphur oxides react to the highly corrosive nitric and sulphuric acid with water vapour. The classification of BSG as fuel depends on the local legislation which induces dedicated emission standards. For most countries, the combustion of BSG exceeds the legal threshold for dust, CO, NOx, and SOx (BFJ, 2013). A comprehensive and therefore expensive flue gas purification would be mandatory. Calculating with 4 kg BSG DW hL−1, it results in 22.36 kWh hL−1 beer as heat energy before deducting the energy needed to reduce the water content.
Nutritional
Feed
The high fibre and protein content of BSG makes it an excellent source of feed, but the microbial load, pH value, and fermentable sugar contributes to a susceptibility to spoilage and degradation. If BSG is used as a feed without further processing, livestock in the proximity to the brewery is needed to distribute it in a timely manner.
Before the distribution of BSG as animal feed is allowed, various limits for contaminants must be fulfilled. Legal basis for the assessment of marketability of feed in Germany are the Food and Feed Code and the Feed regulation. In the EU, there are the regulations 68/2013, 178/2022, 215/186, 396/2005, 574/2011, 767/2009, 1275/2013, and 2019/1869, as well as the directive 2002/32/EG. The directive establishes the limits for undesirable substances in feed like toxic metals (As, Pb, Hg, Cd), mycotoxins, pesticides, PCB, polycyclic aromatic hydrocarbon, endosulfan, and dioxins, while the regulations updated the respective rejection limits. The regulation 178/2022 states that feed shall not have an adverse effect on human or animal health, which induces the control of Salmonella spec.
A European brewery which wants to sell their BSG as feed needs to be authorised as a feed manufacturer according to the regulation (EC) No 183/2005 of the European Parliament for feed hygiene and registered into a national data base.
Direct feeding
Analysed data for Germany from 2014 to 2022 showed that the mean feed source for livestock can be divided into three major groups: primary feeds, plant-based feed (PBF) by-products, and non-marketable feed. While the latter makes over half of all the feed. BSG must compete with other high-protein plant-based feed from food production and plays only a minor behind press cake from soybean oil production and dried flakes from sugar beets (BLE, 2023). Seasonal fluctuations in beer production and PBF are both going up in the summer which makes it harder for BSG to compete and reduces its market value due to oversupply.
Modern cows with milk yield over 30 kg day−1 need a specialised diet with a balanced energy and protein ratio. The energy is expressed as net energy content for lactation, while the protein is divided into crude protein (XP), usable crude protein (nXP), and non-degradable feed protein (UPD). The latter effects the RNB. By varying the proportion of XP, nXP, and UPD in the feed, the supply of amino acids going into the small intestine is controlled. Deviations from the optimum supply have a detrimental effect on the milk yield (Alert, 2013).
BSG contains on average 35% UPD (Kirchgessner, 2011), which limits its applicability as feed. The recommended maximum dosage varies depending on the source between 7.5% and 20 kg BSG per day and cow (Jeroch et al., 2008; LFL, 2008). Calculating with 12 million cows in Germany (BMEL, 2020), these results in a potential maximal demand of 33–88 Mt BSG feed per year which exceeds the actual amount of BSG produced in Germany (80 million hL times 20 kg BSG hL−1 equals 1.6 Mt BSG) by a factor of 20 to 55. This calculation will be different for every country because of the large deviation of beer consumption, cattle husbandry, and their geographical proximity. What stays is that the beer consumption would need to exceed the consumption of dairy products and cattle meat by far to get a surplus of usable BSG. The problem rather occurs through seasonal fluctuations which influence the need for BSG as feed antagonistic to the beer production. There is a surplus of green fodder in the summer, while the beer production and therefore the BSG production is at its peak, which results in less demand for BSG and could release usable BSG for valorisation processes.
Ensiling
If no direct distribution of the BSG as feed is possible, it needs a way to increase the shelf life and still obtain the usability as a feed source. This is possible through ensiling. Since the brewing process is specialised on extracting fermentable carbohydrates from the malt, the BSG is therefore low on it with about 10–12 g kg−1 which is lower than the recommended quantity of 30 g kg−1 fermentable carbohydrates for other PBF to ensure successful ensiling. Contrary to the resulting expectation of a failing ensiling, it is nevertheless successful. The author Weber (2009) explained it through two main mechanisms: the high amount of lactic acid bacteria and the low buffer capacity of the BSG. Lactic acid bacteria are part of the natural microflora of malt and increased through the malting process. After a heat-induced log reduction in the late mashing process, the amount of colony-forming units of lactic acid bacteria rises again after the cool down of the BSG, consisting of hetero- and homofermentative lactic acid bacteria which decompose the reluctant LC into fermentable sugars and, through the production of lactic acid (LA), reduce the pH value of the silage. The low buffer capacity with about 32 g LA kg−1 BSG DW to reduce the pH value to 4.0 ensures a rapid drop in the pH value and prevents the ensiling process from turning into a rotting process. The low buffer capacity is a result of a low ammonia content, since the soluble nitrogen substrates are already extracted during the mashing process and a well-balanced acidic and alkaline salts content in the BSG (Table 4) (Weber, 2009).
BSG can either be ensiled after pressing or directly through a film tube silage in hermetic plastic bags. While the pressing increases the DW to 20%–30%(w/w), the feed value, and the ensilability, it produces a high COD presswater which needs further processing or disposal (Milew et al., 2022). The film tube silage enables a direct hermetic packaging directly from the brewery with minimal risk of contamination, no additional silo requirement on the farmer's premises, and less edge and surface losses (Steinhöfel, 2004; Weber, 2009). The hermetic sealed tubes conceal the silage effluent which is negative proportional to the DW of the silage substrate, so BSG contains a lot of it which needs to be removed after ensiling.
Food
BSG with the high LC content is rich in dietary fibres like arabinoxylan and β-glucan, protein, minerals, and polyphenols. Polyphenols like the hydroxycinnamic acid and ferulic acid function as a potent antioxidant while their content is influenced by the malting technique. Birsan et al. (2019) measured fourfold higher values in light malt than in dark malt. The high nitrogen content of BSG in the form of proteins and amino acids at 22%(w/w) accounts for a significant portion of BSG (Herfellner et al., 2006). The main protein fractions are albumin, globulin, glutelin, and hordein, which are associated with anti-inflammatory and antioxidative health benefits (Wen et al., 2019), and are high on the essential amino acid lysine in contrast to other cereals (Lynch et al., 2016). Calcium, magnesium, iron, and phosphorus are present in BSG in nutritionally relevant amounts as shown from Mussatto et al. and own measurements (Table 4, Mussatto et al., 2006). A food product enriched with BSG will gain all the health benefits associated with fibres, polyphenols, minerals, and essential amino acids. BSG can therefore be considered as an important ingredient for functional foods (Table 3) (Fărcaş, 2014; Lynch et al., 2016; Verni et al., 2020).
Food product . | Reference . |
---|---|
Cereal bars | Stelick et al. (2021) |
Cheese | Abd El-Moneim et al. (2018) |
Chips | Garrett et al. (2021) |
Cookies/biscuits | Fărcaș et al. (2021), Guo et al. (2014) |
Edible mushrooms | Weber (2009) |
Low alcohol beer | Canonico et al. (2023) |
Muffins | Combest et al. (2020) |
Pasta | Schettino et al. (2021), Nocente et al. (2019) |
Yoghurt | Naibaho et al. (2022) |
Food product . | Reference . |
---|---|
Cereal bars | Stelick et al. (2021) |
Cheese | Abd El-Moneim et al. (2018) |
Chips | Garrett et al. (2021) |
Cookies/biscuits | Fărcaș et al. (2021), Guo et al. (2014) |
Edible mushrooms | Weber (2009) |
Low alcohol beer | Canonico et al. (2023) |
Muffins | Combest et al. (2020) |
Pasta | Schettino et al. (2021), Nocente et al. (2019) |
Yoghurt | Naibaho et al. (2022) |
Food product . | Reference . |
---|---|
Cereal bars | Stelick et al. (2021) |
Cheese | Abd El-Moneim et al. (2018) |
Chips | Garrett et al. (2021) |
Cookies/biscuits | Fărcaș et al. (2021), Guo et al. (2014) |
Edible mushrooms | Weber (2009) |
Low alcohol beer | Canonico et al. (2023) |
Muffins | Combest et al. (2020) |
Pasta | Schettino et al. (2021), Nocente et al. (2019) |
Yoghurt | Naibaho et al. (2022) |
Food product . | Reference . |
---|---|
Cereal bars | Stelick et al. (2021) |
Cheese | Abd El-Moneim et al. (2018) |
Chips | Garrett et al. (2021) |
Cookies/biscuits | Fărcaș et al. (2021), Guo et al. (2014) |
Edible mushrooms | Weber (2009) |
Low alcohol beer | Canonico et al. (2023) |
Muffins | Combest et al. (2020) |
Pasta | Schettino et al. (2021), Nocente et al. (2019) |
Yoghurt | Naibaho et al. (2022) |
. | mg kg−1 . | . | mg kg−1 . | . | mg kg−1 . |
---|---|---|---|---|---|
Phosphorus | 3,272 | Molybdenum | 0.2 | Cadmium | <0.04 |
Potassium | 15.6 | Silicon | 241 | Tin | <0.10 |
Nitrogen | 41,600 | Strontium | 0.14 | Nickel | <0.04 |
Calcium | 39.5 | Boron | 0.44 | Chromium | <0.04 |
Magnesium | 29.5 | Arsenic | <0.04 | Manganese | 0.9 |
Sodium | 1.3 | Antimony | <0.04 | Zink | 2.9 |
Iron | 215 | Selenium | <0.04 | Barium | 0.7 |
Copper | 6.4 | Lead | <0.04 | Cobalt | <0.2 |
. | mg kg−1 . | . | mg kg−1 . | . | mg kg−1 . |
---|---|---|---|---|---|
Phosphorus | 3,272 | Molybdenum | 0.2 | Cadmium | <0.04 |
Potassium | 15.6 | Silicon | 241 | Tin | <0.10 |
Nitrogen | 41,600 | Strontium | 0.14 | Nickel | <0.04 |
Calcium | 39.5 | Boron | 0.44 | Chromium | <0.04 |
Magnesium | 29.5 | Arsenic | <0.04 | Manganese | 0.9 |
Sodium | 1.3 | Antimony | <0.04 | Zink | 2.9 |
Iron | 215 | Selenium | <0.04 | Barium | 0.7 |
Copper | 6.4 | Lead | <0.04 | Cobalt | <0.2 |
. | mg kg−1 . | . | mg kg−1 . | . | mg kg−1 . |
---|---|---|---|---|---|
Phosphorus | 3,272 | Molybdenum | 0.2 | Cadmium | <0.04 |
Potassium | 15.6 | Silicon | 241 | Tin | <0.10 |
Nitrogen | 41,600 | Strontium | 0.14 | Nickel | <0.04 |
Calcium | 39.5 | Boron | 0.44 | Chromium | <0.04 |
Magnesium | 29.5 | Arsenic | <0.04 | Manganese | 0.9 |
Sodium | 1.3 | Antimony | <0.04 | Zink | 2.9 |
Iron | 215 | Selenium | <0.04 | Barium | 0.7 |
Copper | 6.4 | Lead | <0.04 | Cobalt | <0.2 |
. | mg kg−1 . | . | mg kg−1 . | . | mg kg−1 . |
---|---|---|---|---|---|
Phosphorus | 3,272 | Molybdenum | 0.2 | Cadmium | <0.04 |
Potassium | 15.6 | Silicon | 241 | Tin | <0.10 |
Nitrogen | 41,600 | Strontium | 0.14 | Nickel | <0.04 |
Calcium | 39.5 | Boron | 0.44 | Chromium | <0.04 |
Magnesium | 29.5 | Arsenic | <0.04 | Manganese | 0.9 |
Sodium | 1.3 | Antimony | <0.04 | Zink | 2.9 |
Iron | 215 | Selenium | <0.04 | Barium | 0.7 |
Copper | 6.4 | Lead | <0.04 | Cobalt | <0.2 |
Up to 10%(w/w) of wheat flour can be replaced by BSG without adversely alternating the physical properties of the final cereal product like pasta and bread and still profiting from the health benefits of BSG (Gupta et al., 2010). Those 10%(w/w) BSG will increase the protein content of the product by 50%(w/w), essential amino acids by 10%(w/w), and doubling the amount of fibre (Fărcaş, 2014). This fibre is the main component of BSG with a content of 36–52%(w/w) LC and responsible for the change in texture of BSG-enriched food products which tends to harden or become more viscous (Naibaho et al., 2022). The maximum amount of BSG enrichment can vary from 6%(w/w) in yoghurt to 50%(w/w) in cheese (Abd El-Moneim et al., 2018) while the added health beneficial ingredients correlate linear with it.
While lautering, the malt is not completely exhausted from fermentable sugars and free amino acids. Depending on the lautering process and the amount of rinse out, there could be enough fermentable material to produce low alcoholic beverages. The authors (Canonico et al., 2023) produced such a recycled wort containing glucose 0.67 g L−1, sucrose 1.7 g L−1, and maltose 9.7 g L−1, and 47.11 mg N L−1. Other authors used the fibre-rich BSG for yoghurt fermentation. The LC addition of BSG accelerates the fermentation process due to increased arabinoxylans, β-glucans, and prebiotic LC. After fermentation, the yoghurt showed increased viscosity and shear stress compared to a non-enriched yoghurt (Naibaho et al., 2022). While the susceptibility for microbial decomposition of BSG is a disadvantage for many technical and distributional purposes, the moisture, protein, and carbohydrate content make it a good cultivation medium for microorganisms, either for the production of edible mushrooms (Weber, 2009) or the biotechnology approaches to produce enzymes (Xiros & Christakopoulos, 2012).
Barley can be contaminated with mycotoxins from the Fusarium and Aspergillus genus, like deoxynivalenol, nivalenol, zearalenone, T-2, HT-2, fumonisins, aflatoxins, and ochratoxin A, which can be found throughout the entire production process from harvesting, over the malting and mashing process (Katharina Habler, 2016). Mycotoxins that are not extracted during the mashing process will be present in the BSG and every further step of the production chain (Saba et al., 2019). If BSG is to be sold as food, the legal thresholds for mycotoxins and other contaminants must be complied with.
Composting
It is possible to compost BSG, press cake, or fermentation digestate from a biogas plant directly if they are mixed with the right additives (Assandri et al., 2020; Rehl and Müller, 2011). While composting, the organic matter of BSG is broken down by microorganisms under aerobic and exothermic conditions. Through oxidative chemical and microbiological decomposition of the organic polymer matrix, humic substances originate from the BSG. After the final humification and mineralisation process, the original weight is reduced, organic pollutants are removed, and nutrients are enriched. Because of the low C/N ratio, high-moisture content and pH value, BSG cannot be composted directly and needs a carbon-rich source (e.g., straw, wood chips, sawdust) as well as manure to start the process (Assandri et al., 2020). Other authors described the direct usage of BSG mixed with mineral fertiliser (Assandri et al., 2020), composted material (Aboukila et al., 2018), with cow manure, or with worms to produce vermicompost (Saba et al., 2019). Own measurements with ICP-OES after a microwave-assisted nitric acid digestion of BSG obtained from the Bayerische Staatsbrauerei Weihenstephan in 2022 showed that it is rich in two of the three main components of mineral fertiliser nitrogen and phosphorus but not potassium. Correctly composted BSG with added carbon and some minerals could replace more expensive and not sustainable chemical fertiliser (Chrysargyris et al., 2013; Papamichalaki et al., 2014). Composting is an aerobic state and the fermentation gases are not used which lead to odour nuisance. The obtained fertiliser would need to be compared against the digestate from a biogas plant which has the same minerals but less biomass and a different C/N ratio.
Source . | . | Electrical . | Heat . | Combined . |
---|---|---|---|---|
Waltenberger (2023) | Biogas | n.a. | n.a. | 0.727 |
Sganzerla et al. (2022a) | Biogas | 0.133 | 0.166 | 0.300 |
Buller et al. (2022) | Biogas | 0.230 | 0.333 | 0.563 |
Dudek et al. (2019) | Biogas | n.a. | n.a. | 0.536a |
Gil-Castell et al. (2022) | Combustion | n.a. | 1.025 | 1.025b |
Wagner et al. (2022) | Bioethanol | n.a. | n.a. | 1.634c |
Source . | . | Electrical . | Heat . | Combined . |
---|---|---|---|---|
Waltenberger (2023) | Biogas | n.a. | n.a. | 0.727 |
Sganzerla et al. (2022a) | Biogas | 0.133 | 0.166 | 0.300 |
Buller et al. (2022) | Biogas | 0.230 | 0.333 | 0.563 |
Dudek et al. (2019) | Biogas | n.a. | n.a. | 0.536a |
Gil-Castell et al. (2022) | Combustion | n.a. | 1.025 | 1.025b |
Wagner et al. (2022) | Bioethanol | n.a. | n.a. | 1.634c |
Energy content with the assumption of 50%(vol/vol) CH4 in the biogas.
Energy required for drying is not deducted.
Heating value of the produced bioethanol, without deducted energy of production.
Source . | . | Electrical . | Heat . | Combined . |
---|---|---|---|---|
Waltenberger (2023) | Biogas | n.a. | n.a. | 0.727 |
Sganzerla et al. (2022a) | Biogas | 0.133 | 0.166 | 0.300 |
Buller et al. (2022) | Biogas | 0.230 | 0.333 | 0.563 |
Dudek et al. (2019) | Biogas | n.a. | n.a. | 0.536a |
Gil-Castell et al. (2022) | Combustion | n.a. | 1.025 | 1.025b |
Wagner et al. (2022) | Bioethanol | n.a. | n.a. | 1.634c |
Source . | . | Electrical . | Heat . | Combined . |
---|---|---|---|---|
Waltenberger (2023) | Biogas | n.a. | n.a. | 0.727 |
Sganzerla et al. (2022a) | Biogas | 0.133 | 0.166 | 0.300 |
Buller et al. (2022) | Biogas | 0.230 | 0.333 | 0.563 |
Dudek et al. (2019) | Biogas | n.a. | n.a. | 0.536a |
Gil-Castell et al. (2022) | Combustion | n.a. | 1.025 | 1.025b |
Wagner et al. (2022) | Bioethanol | n.a. | n.a. | 1.634c |
Energy content with the assumption of 50%(vol/vol) CH4 in the biogas.
Energy required for drying is not deducted.
Heating value of the produced bioethanol, without deducted energy of production.
Discussion
As shown by many scientific authors and compiled in this review, the potential utilisations methods for BSG are abundant. Separated into the fields of material production, energy recovery, and nutritional use, it is hard to find a comparative value, but it should be clear that a final disposal in a landfill must be avoided and BSG is integrated into a circular economy.
The high-water content of BSG and microbial susceptibility right out of production can be used as an advantage for the use in a biorefinery. From biofuels ethanol or 2–3-butanediol, bioplastic precursors polyhydroxyalkanoates, or biotechnological enzymes, BSG can be a suitable substrate. The cellulose fraction could potentially replace food waste. On the other hand, the highly reluctant LC biomatrix requires physicochemical pretreatments to increase the yields which further produces problematic WW and counteracts the sustainable approach. To extract and decrystallise the cellulose fraction from the protein, lignin, and hemicellulose fractions, a pretreatment like in the paper industry with alkaline, acidic, or ionic liquids would be needed. Those pretreatments saccharify the LC biomass to provide fermentable sugars for microorganism like Escherichia coli, Saccharomyces cerevisiae, and Zymomonas mobilis which generate problematic waste and would only use a fraction of the BSG (Fernández-Sandoval et al., 2019; Vargas-Tah et al., 2015; Wagner et al., 2022). The use of BSG as an aggregate in brick firing, for HTC, or as a packaging material are rather negligible. It is possible to use BSG for those processes, but it does not offer any advantage over other LC biomass by-products like straw and saw dust that can be used as substitutes. A biogas plant can ferment BSG into biogas to generate heat and electricity for the brewery, as well as digestate rich in minerals, phosphate, and nitrogen which can be sold as fertiliser. The Gösser-Brauerei AG achieves an annual biogas production of 2.2 Mm3 using 16,500 t of BSG, corresponding to a total energy content of 12 GWh (Waltenberger, 2023). This translates to approximately 0.133 m3 of biogas with 0.727 kWh of energy per kilogram of BSG, or 2.66 m3 of biogas with 14.54 kWh energy per hL beer. From the sustainability reports of seven different German breweries, an average energy consumption of 10.3 kWh hL−1 electrical and 34.9 kWh hL−1 thermal energy is deduced (Andechs, 2021; Augustiner, 2022; Brauerei S. Riegele I. R. K., 2022; Lammsbräu, 2023; München, 2020). Without differentiating between thermal and electrical energies, a potential of about 32% of the total energy usage could be covered. One must be careful when reading about energy numbers because some authors do not declare if their numbers are based on wet or DW of BSG and how much energy is useable rather than needed to prepare the BSG or maintain the production. In Table 5, different energy yields from biogas, direct combustion, and bioethanol are stated and they diverge strongly. Sganzerla et al. calculates a return on investment of 23.68% for a biogas plant if all the energy is used and the digestate sold as a fertiliser. Energy prizes are highly depending on the country, industry, and geopolitics. The energy demand of a brewery on the other side depends on its state of the art and utilisation. When a biogas plant pays off is very individual, but it would make a brewery in every case more energy independent, decrease its waste, and generate income. The main problem of a biogas plant is the exponential scaling of the clean-up and production cost. While most breweries in Europe are small to medium businesses, they do not reach a BSG mass flow to obtain competitive gas prices or do not have the place for a fermenter. If the BSG is instead directly combusted, the useful heat energy would be higher, but the generated emissions would not meet modern standards. If the water reduction is done energy efficiently by pressing, the presswater arises as a high COD WW.
When used in cereal food products, BSG competes with other cereal by-products high in fibre and protein-like oat and wheat bran which are well established and already dried with a good shelf-life. BSG offers neither health nor technological advantages over those but lacks the storage capability because of the high-moisture content and microbial susceptibility, and can only be added in small quantities. Dairy food products like cheese and yoghurt could benefit more from BSG with its prebiotic and rheological properties. When it comes to the utilisation as animal feed, BSG can be fed directly or ensiled for later use. The direct and silage feeding of BSG are already established and the predominant application. BSG is rich in protein, cheap, and a local biomass which needs no import from abroad and can replace press cake from the vegetable oil production. An issue arises from the simultaneous peak production of green fodder and BSG during the summer, leading to a temporary oversupply and a consequent reduction in market value. To get rid of the BSG to continue production, composting would be possible. Compared to the biogas plant, the technological prerequisites are low but the heat energy of the exothermic aerobic fermentation and emerging gases are not used but rather adversely affect the environment. Additionally supplements in the form of a high carbon biomass and manure are needed to start the composting process. The final product can be sold as a fertilizer comparable to the biogas plan digestate.
When used as a biosorbent, BSG has the highest valorisation potential and the redesign of the biowaste into a biosorbent can help to clean-up industrial WW in developing countries. The demand for adsorbents for water remediation worldwide is high. The most used adsorbent is activated carbon with a worldwide consumption of about 1.1 Mt yearly with a ratio of 85/15 between non-renewable coal base and renewable resources (Ragan & Megonnell, 2011), which is small compared to 7.6 MT BSG DW, respectively. Activated carbon is a highly expensive and non-renewable when made from coal and in need for high energy when made from biowaste (carbonisation). As shown in Functional materials and Biosorbents sections, it is possible to produce effective biosorbents from LC high biowaste like BSG. The mashing process in the brewery is already a good clean-up pretreatment, and the reduced lignin content of BSG compared to other plant-based biowaste improves its reactivity. The press and wash water that arises in the pretreatment process is high in COD and phosphate which both need to be recovered and could be combined with a biogas plant.
Conclusion
The world is in a high demand for sustainable biosorbents for the remediation of WW and its implementation would help to realise a circular economy when coal-based and non-biological technical adsorbents are replaced. LC-based materials offer a great potential for that application and have already been proven to be effective biosorbents. Through the brewing process, the BSG is mashed and extracted from small soluble molecules, thereby rendering it suitable for further processing steps to become a biosorbent, an advantage it holds over other forms of biowaste. In contrast to the other utilisation methods such as biogas, animal feed, and food, where BSG offers no significant benefits over existing plant-based biowaste already in use but rather poses additional technological or legal obstacles. The production of biosorbents from BSG is therefore seen as the most promising utilisation method.
Outlook
What needs to be studied is the life cycle of a BSG biosorbent. If the goal is to close the circle and obtain all resources in our economy, the disposal of a used and metal-loaded BSG biosorbent on a landfill would contradict the efforts made before. Depending on the adsorbed metal, the use case will differ. Fe and Mn could be recovered from ashes after incineration. Zn-enriched BSG would be a value-added feed. Pb, Cd, or other high toxic metal-enriched BSG biosorbents would need an exhausting regeneration before further use. If it were possible to regenerate the BSG biosorbents completely from any adsorbed contaminant, a reintroduction of the BSG biosorbent in every other utilisation method explained above would be possible again. To clarify the question of the life cycle assessment of a BSG biosorbent and its suitability for WW remediation, further studies are in progress.
Data availability
The data that support the findings of this study are available on request from the corresponding author.
Author contributions
Philipp Dancker (Conceptualization [lead], data curation [lead], investigation [equal], resources [lead], visualization [lead], writing—original draft [lead], writing—review & editing [equal]), Karl Glas (Conceptualization [equal], investigation [equal], supervision [equal], writing—review & editing [equal]), and Martina Gastl (Conceptualization [equal], investigation [equal], supervision [equal], validation [equal], writing—review & editing [equal]).
Funding
None declared.
Conflicts of interest
The authors declare that they have no known competing financial interests or personal relationships that could have appeared to influence the work reported in this review.