-
PDF
- Split View
-
Views
-
Cite
Cite
P A Guerrero-Seañez, C G Garay-Reyes, A Martínez-García, X Atanacio-Sánchez, I Estrada-Guel, J M Mendoza-Duarte, R Martínez-Sánchez, Effect of Sc Addition on Microstructure and Hardness of 2024 Al Alloy, Microscopy and Microanalysis, Volume 29, Issue Supplement_1, 1 August 2023, Pages 2026–2027, https://doi.org/10.1093/micmic/ozad067.1048
- Share Icon Share
2024 alloy is one of the most prominent Al alloys, with Cu as the primary alloying element. Due to its high strength and fatigue resistance, 2024 alloy is widely used in aircraft, especially in stressed wing and fuselage structures and aircraft accessories [1-3]. Sc-modified Al alloys represent a generation of high-performance alloys that represent numerous advantages over high-strength Al alloys since they exhibit significant grain refinement, strengthen welds, and eliminate hot cracking in welds. In addition, it has been possible to achieve an ideal combination of strength, density, and thermal stability due to the unique precipitation-hardening characteristics of Sc [4]. On the other hand, liquid metallurgy processing involves adding particles externally to the molten metal or synthesizing during the alloy melting process. The former is called ex-situ fabrication, while the latter is called in-situ fabrication. The advantages of in-situ fabrication allow for obtaining a small size of reinforcing particles, good interfacial bond strength, uniform particle distribution, thermodynamically stable particles, and low processing cost [5].
2024 alloy was melted with a master alloy Al-Sc containing 2 wt. % Sc for obtaining a composition of 0.4 wt. % Sc. After, the alloy was hot-extruded at 500 °C with an extrusion ratio of 16 by indirect extrusion. Later, a T6 heat treatment was carried out, which included a solubilization treatment at 493 °C for 4 h, quenching in water at room temperature, and artificial aging at 180 °C for 30, 60, 300, 600, 3000, and 6000 min. The process was also followed for an unmodified 2024 alloy (reference). The microstructural characterization was carried out by scanning electron microscope HITACHI SU3500. The hardness was evaluated by Vickers microhardness and Rockwell hardness tests. The first was measured following the ASTM E92 standard using a LECO LM300 AT tester, and the second was measured following the ASTM E18 standard using a Wilson C503 R tester in the HRB scale.
Fig. 1 shows micrographs obtained by SEM, and Fig. 2 represents the results of microhardness and microhardness in every condition. It can be observed that the undissolved Cu in the alloy segregates across the grain boundary, and the Sc added forms new compounds with the Cu and Mg from the alloy. This is shown by the difference in Cu content in the extruded and solubilized samples meaning the Cu in the new phase created with the added Sc does not get into the solid solution. Through the hardness results, we conclude that the new phases generated by added Sc improve hardness in the as-cast and extruded condition but restrict the hardening capabilities of the solubilization and aging process due to the lack of Cu in the solid solution.

SEM-BSE micrographs and EDS of the 2024 (a) and 2024-0.4 wt. % Sc (b) samples in As-Cast, Extruded and Solubilized Condition.
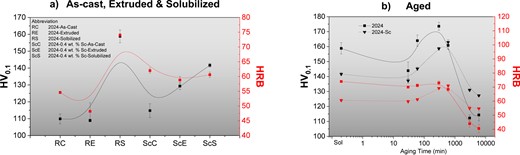
a) Vickers and Rockwell hardness in As-cast, Extruded & Solubilized condition. b) Vickers and Rockwell hardness during aging treatment.