-
PDF
- Split View
-
Views
-
Cite
Cite
Cheng Zhu, The influence of cement-based composite materials on the performance of bridges: modification and optimization by nano-SiO2 material, International Journal of Low-Carbon Technologies, Volume 15, Issue 3, August 2020, Pages 409–413, https://doi.org/10.1093/ijlct/ctaa012
- Share Icon Share
Abstract
Cement-based materials have been widely used in bridge construction. In order to further improve their performance, this study analyzed the modification and optimization functions of nano-SiO2 materials, designed test specimens with different content of nano-SiO2 and conducted experiments on their flow performance, compression resistance, bending resistance and impermeability. The results showed that the flow performance of the materials decreased and the impermeability decreased with the increase of nano-SiO2 content. The compressive strength and flexural strength are the best when the content of nano-SiO2 is 1%. On the whole, the best content of nano-SiO2 is 1%; when the content of nano-SiO2 is 1%, all the properties of the specimens are good, which is more conducive to the construction of bridges in various complex environments. The research in this paper has made some contributions to the further application of nano-SiO2 in the optimization of building materials, which is conducive to the better development of building materials.
1. INTRODUCTION
Cement-based materials (concrete, mortar, etc.) are easy to manufacture and low in cost. They have been widely used in fields such as tunnel [1], railway [2], road and bridge [3]. The strength and durability of materials are important indexes to evaluate the quality of materials. With the application of building materials in more fields and more environments, the improvement of comprehensive performance of cement materials has attracted more and more extensive attentions. The emergence of nanomaterials provides a new way to further improve the performance of materials, which is widely used in the modification and optimization of materials such as mortar and concrete. Li et al. [4] studied the role of carbon nanotubes (CNTs) in improving cement composites and found that CNTs might accelerate cement hydration and increase the friction between CNTs and cement matrix. Ma et al. [5] studied the effect of nano-TiO2 in cement mortar and found by means of a scanning electron microscope and X-ray that 3% nano-TiO2 could significantly improve the tensile and flexural strength of cement mortar, the internal porosity and harmful porosity of mortar decreased by 37.0% and 37.9%, respectively, at 28 days, and the compactness was effectively improved. Cao et al. [6] found that the addition of 0.02% functional fossil graphene nano tablets could accelerate the hydration reaction and significantly improve the bending and compressive strength of cement materials. Czechowska et al. [7] found that nano TiHA could affect the solidification and hardening of cement, chitosan could delay the solidification of calcium sulfate dihydrate and the combination of them with calcium sulfate could improve the treatment and processability of cement. Aiming at the application of cement-based composite materials in bridges, nano-SiO2 was used for modifying and optimizing cement-based composite materials in this study, so as to improve the application effect of those materials in bridges.
2. NANOMATERIALS
Nanomaterials play an important role in medicine, military, architecture and environment. They have the following characteristics:
(1) Small size effect. Due to the small size, the acoustic, optical and thermal properties of nanomaterials have changed greatly [12].
(2) Surface effect [13]. The surface binding energy and chemical properties of nanomaterials have been significantly improved, and they have unique advantages in catalysis and adsorption.
(3) Macroscopic quantum tunneling effect [14]. The properties of nanoparticles can change through the barrier of the macroscopic system.
(4) Quantum size effect [15]. The energy level gap of nanomaterials is large.
Nano-SiO2 has been widely used in the optimization of building materials. Nano-SiO2, a kind of white amorphous particles, has characteristics of small mass and good high-temperature resistance. Compared to other nanomaterials, nano-SiO2 has excellent chemical reactivity, smaller geometric dimension and larger specific surface area. It can rapidly react with calcium hydroxide to generate hydrated calcium carbonate to promote the hydration reaction of materials and improve material properties. Nano-SiO2 has outstanding performance in the modification of materials such as rubber, plastics and ceramics.
3. MATERIALS AND METHODS
3.1. Necessity of improving bridge performance
With the development of economy, the number of bridges in China is growing. In order to promote the development of the bridge cause, all kinds of new technologies and materials are rapidly developed and applied. However, at the same time, the durability of bridges is also very prominent, and problems such as bridge deck fracture and bridge collapse often occur. Under the action of environment, the mechanical and chemical properties of concrete or reinforcement will change, which will lead to the deterioration of bridge function and failure of normal operation. Therefore, the research and design of new bridge materials and improving the performance of bridges has a very important practical value.
3.2. Materials
Cement: P.O.42.5 ordinary Portland cement, Harbin Swan Cement Plant.
Fly ash: class I fly ash, Nanjing Thermal Power Plant.
Aggregate: medium sand, Yuquan Sand Plant, with 203 fineness modulus; gravel, Binxian Binxi Bedding Plant, with continuous grading.
Superplasticizer: polycarboxylate superplasticizer, Heilongjiang Keman Building Materials Co., Ltd.
Nano SiO2: Hangzhou Wanjing New Material Co., Ltd, and its performance is shown in Table 1.
Water: tap water.
Performance index of nano-SiO2.
Specific surface area/m2/kg | 200 |
Average particle size/nm | 30 |
PH value | 6 |
Apparent density/g/l | 55 |
Specific surface area/m2/kg | 200 |
Average particle size/nm | 30 |
PH value | 6 |
Apparent density/g/l | 55 |
Specific surface area/m2/kg | 200 |
Average particle size/nm | 30 |
PH value | 6 |
Apparent density/g/l | 55 |
Specific surface area/m2/kg | 200 |
Average particle size/nm | 30 |
PH value | 6 |
Apparent density/g/l | 55 |
3.3. Specimen preparation
(1) Mix proportion: the content of nano-SiO2 is 0.5%, 1%, 2% and 3%, respectively, and the mix proportion of test piece is shown in Table 2.
(2) Preparation process: (i) nano-SiO2 was mixed with some water and stirred by a small high-speed mixer for 2 min to obtain the pre-dispersion solution; (ii) dry mix cement, aggregate and fly ash were stirred for 2 min; (iii) the remaining water, pre-dispersion solution and water reducer were added and stirred for 8 min; (iv) the mixture was poured into the mold and put for 1 day, and it was maintained in the standard curing room for 28 days.
Mix proportion of test specimens.
Specimen number . | S0 . | S1 . | S2 . | S3 . | S4 . |
---|---|---|---|---|---|
Cement/kg | 379 | 377.105 | 375.210 | 371.420 | 367.630 |
Fly ash/kg | 95 | 95 | 95 | 95 | 95 |
Sand/kg | 549 | 549 | 549 | 549 | 549 |
Stone/kg | 1222 | 1222 | 1222 | 1222 | 1222 |
Water reducer/g | 4.74 | 4.74 | 7.11 | 9.48 | 9.48 |
Nano-SiO2/kg | 0 | 1.895 | 3.790 | 7.580 | 11.370 |
Water/kg | 166 | 166 | 166 | 166 | 166 |
Specimen number . | S0 . | S1 . | S2 . | S3 . | S4 . |
---|---|---|---|---|---|
Cement/kg | 379 | 377.105 | 375.210 | 371.420 | 367.630 |
Fly ash/kg | 95 | 95 | 95 | 95 | 95 |
Sand/kg | 549 | 549 | 549 | 549 | 549 |
Stone/kg | 1222 | 1222 | 1222 | 1222 | 1222 |
Water reducer/g | 4.74 | 4.74 | 7.11 | 9.48 | 9.48 |
Nano-SiO2/kg | 0 | 1.895 | 3.790 | 7.580 | 11.370 |
Water/kg | 166 | 166 | 166 | 166 | 166 |
Specimen number . | S0 . | S1 . | S2 . | S3 . | S4 . |
---|---|---|---|---|---|
Cement/kg | 379 | 377.105 | 375.210 | 371.420 | 367.630 |
Fly ash/kg | 95 | 95 | 95 | 95 | 95 |
Sand/kg | 549 | 549 | 549 | 549 | 549 |
Stone/kg | 1222 | 1222 | 1222 | 1222 | 1222 |
Water reducer/g | 4.74 | 4.74 | 7.11 | 9.48 | 9.48 |
Nano-SiO2/kg | 0 | 1.895 | 3.790 | 7.580 | 11.370 |
Water/kg | 166 | 166 | 166 | 166 | 166 |
Specimen number . | S0 . | S1 . | S2 . | S3 . | S4 . |
---|---|---|---|---|---|
Cement/kg | 379 | 377.105 | 375.210 | 371.420 | 367.630 |
Fly ash/kg | 95 | 95 | 95 | 95 | 95 |
Sand/kg | 549 | 549 | 549 | 549 | 549 |
Stone/kg | 1222 | 1222 | 1222 | 1222 | 1222 |
Water reducer/g | 4.74 | 4.74 | 7.11 | 9.48 | 9.48 |
Nano-SiO2/kg | 0 | 1.895 | 3.790 | 7.580 | 11.370 |
Water/kg | 166 | 166 | 166 | 166 | 166 |
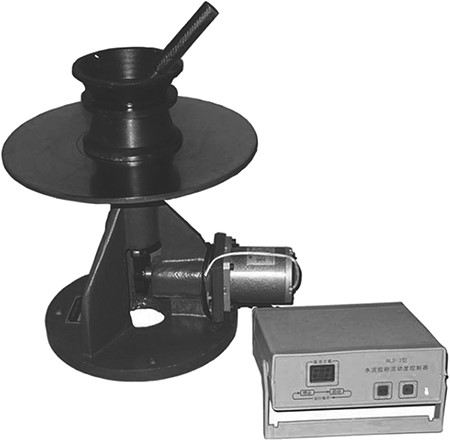
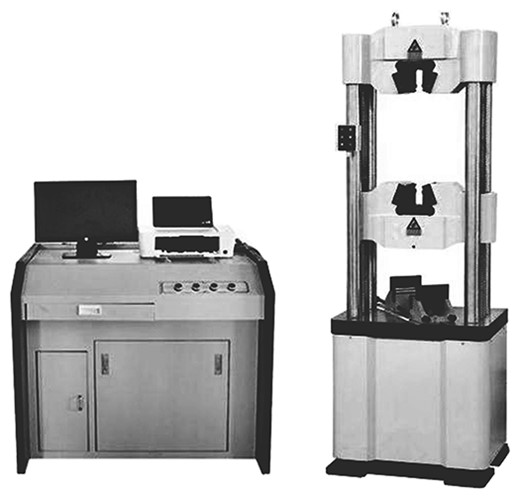
3.4. Performance test
(1) Liquidity test: the fluidity of the mixture was tested using a NLD-3 skip table tester (Figure 1). The main steps were as follows: (i) the tester was wet with wet towel; (ii) the mixture was put into a conical mold in two layers, the first layer was at the site which was 1/2–2/3 of the height of the mold and the second layer was 10~20 mm higher than the mold; (iii) it was quickly pressed to the center using a vibrator, and the surface was smoothed using a spatula; (iv) the mold sleeve was removed, the tester was turned on, and it stopped after 25 times of skips; (v) the diameter of the mixture was measured with a ruler.
(2) Compressive and flexural tests: compressive and flexural tests were carried out using a WE-600b universal testing machine (Figure 2). (i) Compression test: a clamp was selected, the press machine was set as 0, then the test specimen was put into the press machine to make its side compressed, and the loading speed was 2400 N/s ± 200 N/s. The calculation formula of compressive strength was |${R}_{\mathrm{c}}={F}_{\mathrm{c}}/A$|, where |${F}_{\mathrm{c}}$| is the maximum load and |$A$| is the area of the compression surface. (ii) Bending resistance test: the test specimen was put into the clamp to make it being compressed, the positions of the clamp and test specimen were adjusted, the loading speed was 50 N/s ± 10 N/s, and the loading lasted until the test piece was damaged. The calculation formula of flexural strength was |${R}_b=\frac{1.5{F}_{\mathrm{m}}L}{a}$|, where |${F}_{\mathrm{m}}$| is the load in the middle of the test specimen, |$L$| stands for span and |$a$| stands for the side length of the cross section of the test specimen.
(3) Impermeability: (i) the impermeability mold was heated to make it slightly expand; (ii) paraffin was melted to make it being included in the side of the test specimen to prevent water seepage; (iii) the test specimen was pressed into the impermeability mold and installed on the mortar impermeability meter (Figure 3); the test specimen was split after 24 h of continuous compression, and the permeated height was measured.
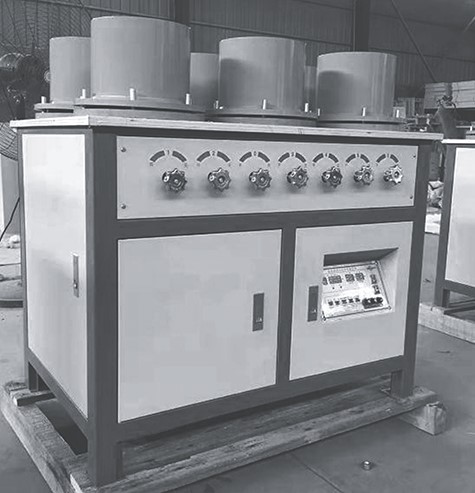
4. RESULTS
4.1. Fluidity
The fluidity of different test specimens is shown in Figure 4.
It was seen from Figure 4 that the fluidity of S0 was 267 mm, while that of S4 was only 152 mm, which was about 43% lower than that of S0, and that of S1 was 251 mm, which had a smaller decrease. The result indicated that the large content of nano-SiO2 would cause a large loss of fluidity.
4.2. Compressive and flexural properties
The compressive and flexural properties of materials have a great impact on the durability of bridges. The better the performance of the materials, the better the use effect in the bridge construction. The compressive and flexural properties of different specimens are shown in Figure 4.
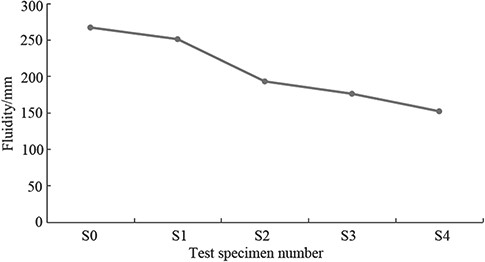
It can be seen from Figure 5 that S2 had the highest compressive and flexural strength, the compressive strength and flexural strength of S0 were 32.5 and 6.8 MPa, respectively, and those of S2 were 49.7 and 10.1 MPa, respectively, which were 52.92 and 48.53% higher than that of S0. It showed that the mechanical properties of the specimens are the best, and they had better performance in bridge construction when the content of nano-SiO2 was 1%.
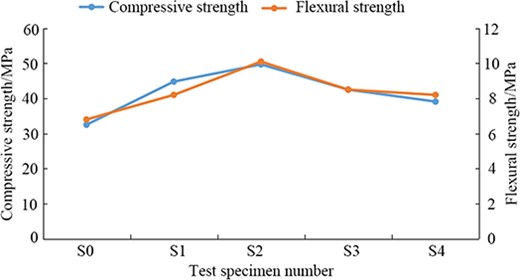
4.3. Impermeability
Corrosion of steel bars will directly cause deterioration of bridges. Therefore, in environments such as coastal and cross sea, the impermeability of bridges is particularly important. The permeated height of different test specimens is shown in Table 3.
. | S0 . | S1 . | S2 . | S3 . | S4 . |
---|---|---|---|---|---|
Permeated height/cm | 3 | 2.94 | 2.81 | 2.03 | 1.67 |
. | S0 . | S1 . | S2 . | S3 . | S4 . |
---|---|---|---|---|---|
Permeated height/cm | 3 | 2.94 | 2.81 | 2.03 | 1.67 |
. | S0 . | S1 . | S2 . | S3 . | S4 . |
---|---|---|---|---|---|
Permeated height/cm | 3 | 2.94 | 2.81 | 2.03 | 1.67 |
. | S0 . | S1 . | S2 . | S3 . | S4 . |
---|---|---|---|---|---|
Permeated height/cm | 3 | 2.94 | 2.81 | 2.03 | 1.67 |
It was seen from Table 3 that the permeated height of the test specimens decreased gradually, the permeated height of S0 was 3 cm and the permeated height of S4 decreased to 1.67 cm, about half of S0, which showed that nano-SiO2 could effectively improve the impermeability of the test specimen and had better applicability in the construction of bridges across the sea and rivers.
5. DISCUSSION
At present, the commonly used concrete materials are prone to crack, erosion and other problems in the use process [16]. With the more and more extensive application of bridges in different regions and environments, how to improve the durability of bridges has also been more and more widely studied, for example, adding fiber materials [17], adding waterproof membrane and reinforcing steel bar [18] and using lightweight concrete [19].
The fluidity of materials refers to the ability of the mixture to overcome the resistance and fill the formwork freely, which has a very important impact on the construction effect. In the practical application of materials, if the fluidity is poor, it may lead to the difficulty of vibration and unable to form, and there will be many holes on the surface and inside the materials, which will affect the construction effect of the bridge. Therefore, it is necessary to study the influence of nano-SiO2 on the fluidity of test specimen. Figure 4 shows that the fluidity of the test specimens was poor when the content of nano-SiO2 was too large, which might be due to the large specific surface area of the amoeba particles. Figure 5 shows that the nano-sized particles were evenly dispersed into the cement paste and effectively filled the gap inside the paste when the content of nano-SiO2 was 1%, but a high content of nano-SiO2 led to the decrease in material properties, which might be because that agglomeration happened to nano-SiO2 and formed a new defect in the paste. It was seen from Table 3 that the higher the content of nano-SiO2, the better the impermeability, which might be because the addition of nano-SiO2 promoted the hydration reaction, thus significantly improving the impermeability of the material. In general, the addition of nano-SiO2 had the greatest impact on the impermeability of the test specimen. The permeated height of S4 was 44.33% lower than that of S0, and it had a great impact on the fluidity of the material. The larger the content of nano-SiO2, the greater the fluidity loss of the material. From this point of view, the content of nano-SiO2 must be appropriate, otherwise it is not conducive to the construction of bridges. Considering from the application of cement-based composite materials in bridges, high compressive and flexural strength is conducive to ensure better working performance of bridges, so that it can better meet the traffic demand of vehicles, etc., and in addition, favorable impermeability can reduce the corrosion rate of internal reinforcement of bridges. Thus, it has a better performance in projects such as cross sea bridges and island construction. In addition to the properties discussed in this paper, the addition of nano-SiO2 also has an impact on the seismic performance of bridges. For example, Zarei et al. [20] investigated the impact of nano-SiO2 and fiber-reinforced polymer on the seismic response of concrete pipes and found that it could reduce the dynamic deflection of the structure, thus reducing the dynamic deformation of the structure. Akbarpour et al. [21] found that the addition of nano-SiO2 could improve the effectiveness of steel fiber reinforced cyclic bending performance in concrete, thus reducing the static load caused by earthquake. Therefore, the influence of nano-SiO2 on the seismic performance of the bridge is worth further study.
Besides, there are some problems that need to be solved in the further research:
(1) Testing the shrinkage, carbonization, heat resistance and frost resistance of the material;
(2) Studying the modification and optimization of nano-SiO2 from the perspective of microstructure;
(3) Exploring the modification of materials by two or more nanoparticles.
6. CONCLUSION
In order to improve the performance of cement-based composite materials in bridge construction, the modification and optimization of nano-SiO2 were studied in this paper. It was found that
(1) the fluidity of the mixture decreased gradually;
(2) the compressive and flexural strength of the specimens increased first and then decreased; when the content of nano-SiO2 was 1%, the mechanical properties of the specimens were the best;
(3) the impermeability of the specimen was improved.
Based on the experimental results, it is concluded that the material have the best properties, can effectively improve the durability of bridges and has a more extensive applicability when the content of nano-SiO2 is 1%.